Special designs in stainless steel for customer-specific requirements & process solutions
Increase quality & safety through perfectly adapted product designs & tools
- Valve flap systems: Optimize production processes with reliable flap systems from CO.RA.®
- Efficient transport systems: Optimize material flow with suitable transport systems from BOLZ INTEC.
- Laboratory cutlery for professionals: Laboratory cutlery in the usual BOLZ INTEC quality.
Sonderkonstruktionen von Behältern & Apparaten aus Edelstahl für spezifische Anforderungen
The design department at BOLZ INTEC designs, plans and develops products according to customer-specific requirements, including containers for pasty substances or liquids, transport containers for hazardous goods, cans for storing and transferring active ingredients, suction hoods for dust-free container loading and much more. In individual production or as small series.
We also manufacture and assemble complete units, such as filling systems for granulates, according to your individual specifications.
Special materials such as Hastelloy can be processed as well as stainless steels.
On request, customer-specific solutions can be developed and supplied from a single source in the usual high BOLZ INTEC quality in conjunction with our competent partners and experienced engineering offices.
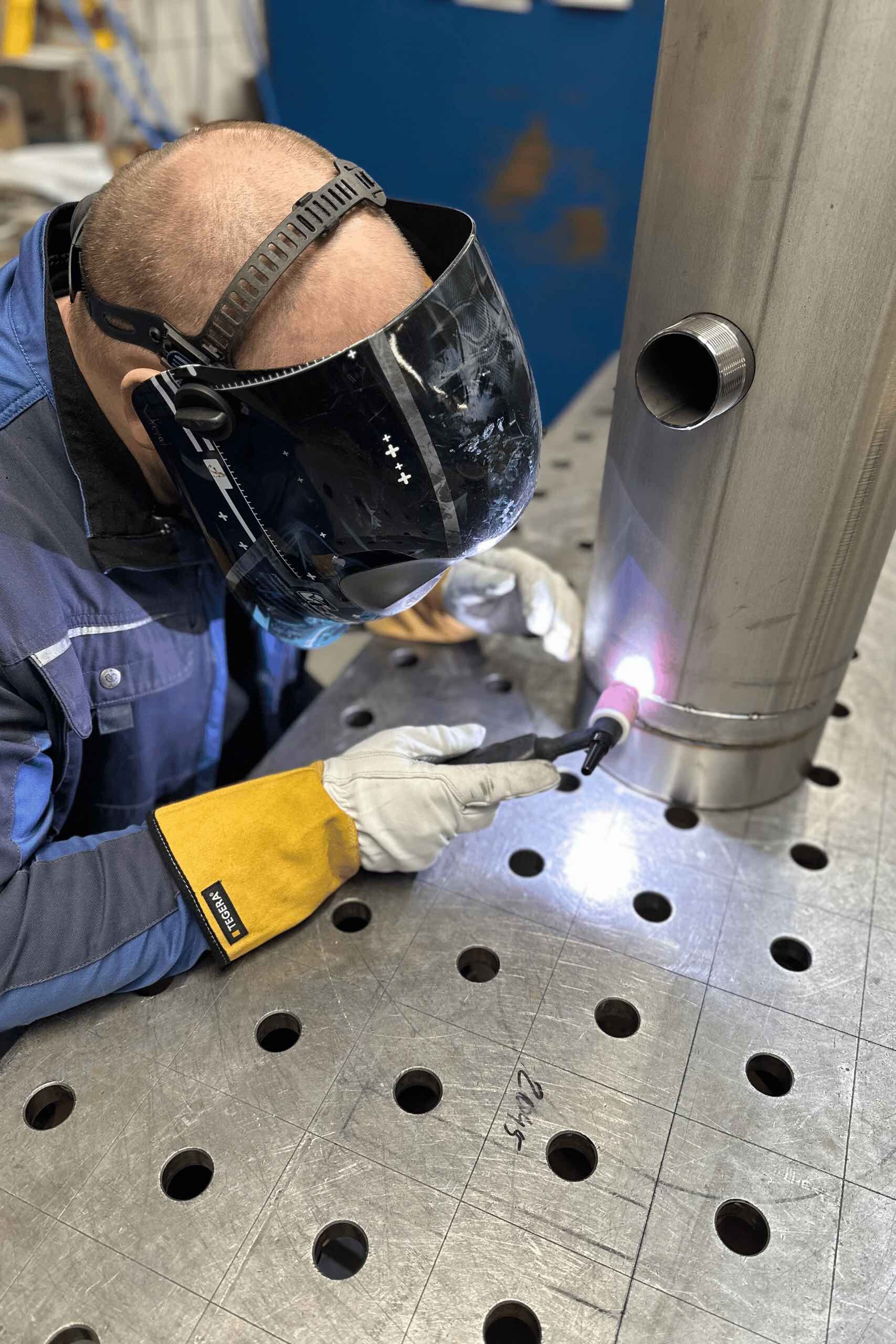
Sonderkonstruktionen - Beispiele
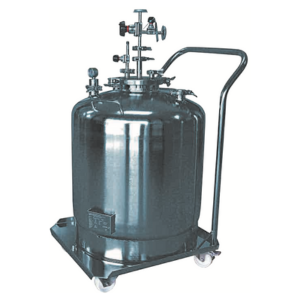
Preparation container for sterile media for transportation / transfer with corresponding container trolley
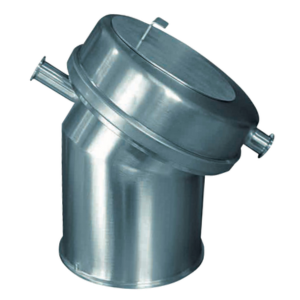
Suction hood for dust-free container loading
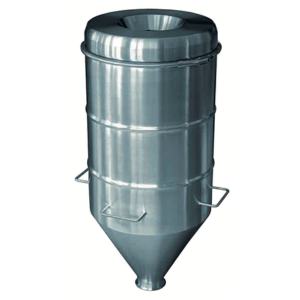
Powder transfer container

Powder transfer can with mandrel gripper holder
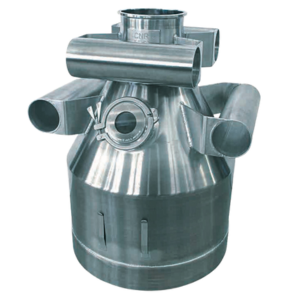
Drug transfer can made of Hastelloy with mandrel gripper holder
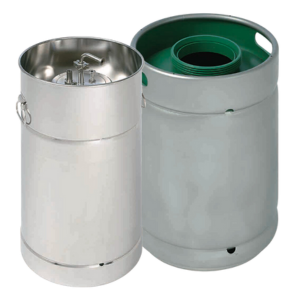
Hazardous goods container Halar-coated
Optimize your processes with CO.RA.® valve flap systems
The GMP-compliant flap systems from CO.RA.® are used in the bulk solids sector for flow control. They are convincing in terms of cost-effectiveness, are characterized by short assembly times, can be dismantled without tools and are therefore easy to clean.
The components of the SOLE VALVE, TABLET VALVE and ROTARY VALVE flap systems are interchangeable without having to replace the entire unit. The inner part is replaced, the outer body remains the same. Operation is simple, reliable and safe.
Since its foundation, CO.RA.® has been dedicated to innovative developments, patenting and the manufacture of components for the pharmaceutical and chemical industries worldwide. CO.RA.® is a leader in the development of new valve and flap systems.
CO.RA.® has been involved in the controlled feeding of systems and dosing of solids in pharmaceutical processes since the 1980s. All products are subject to the strict hygienic requirements of the pharmaceutical industry.
The valve flaps SOLE VALVE®, ROTARY VALVE® and TABLET VALVE® were developed for the flow control of bulk goods (capsules, pills and tablets). SOLVE VALVE® was already established on the market in the 1980s in response to the needs of pharmaceutical customers.
Since the completion of its own sterile room in the 1990s, CO.RA.® has concentrated mainly on the development of filling systems that enable the processing of high containment substances.
CO.RA.® invests resources tirelessly every year in the research and development of products and has been the only company in Italy capable of producing silicone seals under sterile conditions for a year now.
BOLZ INTEC has been the official distributor for Germany since November 2009.
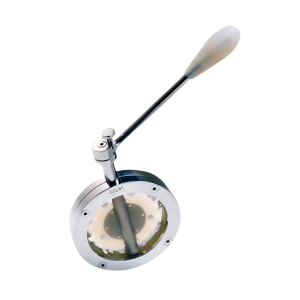
Sole Valve®
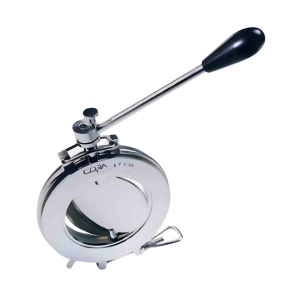
Tablet Valve®
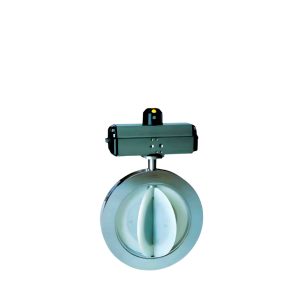
Rotary Valve®
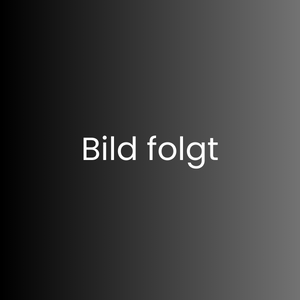
Double Valve®
Butterfly - SOLE VALVE®
for flow control of bulk solids
The butterfly flap is the most widely used flap and covers the widest range of handling applications. SOLE VALVE® has been specially developed for the pharmaceutical, chemical, cosmetics and food industries and is ideal for use in sterile rooms. Each flap is marked with a real batch number, so reordering and traceability in terms of validation are possible at any time.
Applications:
- Unloading and loading of working machine
- Bottom valve for powder, paste and granulate containers
- Blocking sterile air
Features:
- Valve flap in bright stainless steel
- No O-ring seal on the shafts
- Easy to dismantle, check and clean (especially in the version with CLAMP type quick connectors) without the use of tools
- Low weight
- Material: stainless steel and silicone seal
- Ideal for granules, powders and pasty substances
GMP-compliant - Manufacture
All silicone seals are manufactured in a clean room and delivered sealed.
Options:
- Pneumatic positioning device
- Pneumatic actuation types
- Electrical actuation types
Butterfly - TABLET VALVE®
for flow control of bulk solids
TABLET VALVE® have been specially developed for use with tablets/capsules/dragées. The core of the flap is made of VA and is silicone-coated. The outer edge of the silicone disk is soft and flexible so that the product is not damaged when the valve is opened and closed. A batch number is affixed to each flap so that reordering and traceability in terms of validation are possible at any time.
Applications:
- Underneath containers for tablets, capsules, dragées, silicone and gum drops
- For cordoning off fragile products without damaging them
Features:
- Housing: AISI 316 (DIN 1.4401) satin finish
- Flap disk made of stainless steel, silicone-coated
- Shafts without O-ring seals (0R)
- Easy to dismantle, inspect and clean (especially in the version with CLAMP type quick connectors)
- Low weight and small dimensions
- Can be sterilized in an autoclave
- GMP-compliant production
The components of the SOLE VALVE®, TABLET VALVE® and ROTARY VALVE® are interchangeable without having to replace the entire unit.
Here, it is sufficient to replace the movable inner part. The outer body remains the same. This ensures maximum flexibility and low stock levels of spare parts.
Design examples:
- Heavy-duty version "H" with silicone-coated washer but without silicone sealing sleeve
Area of application:- Blocking of heavy or hard dragées or granulates
- To regulate the flow of very small and hard tablets
- Plastic version "K", plastic housing, silicone washer and silicone seal
Area of application:- Where stainless steel is not desirable or cannot be used.
- Inexpensive "E" version without silicone seal, made of AISI 316 stainless steel tube
Area of application:- Granules, empty capsules, coated tablets, tablets
To regulate the flow of very small and hard tablets
- Granules, empty capsules, coated tablets, tablets
Options:
- Double-acting actuator made of stainless steel, electric and pneumatic actuator, Ex version,
- Further options on request
Butterfly - ROTARY VALVE®
for flow control of bulk solids
ROTARY VALVE® allows continuous dosing of the product. Thanks to the star-shaped disk and its 180° back and forth movement, ROTARY VALVE® feeds the corresponding machine and system without material jams or segregation of the product. The speed and dwell time of the Rotary Valve movement can be adapted to the production conditions.
Applications:
- Underneath bulk containers
- For continuous and precise feeding of grinders, tablet presses, capsule fillers, filling systems and sieves with granulates and powder without clogging
Product information:
- Housing: AISI 316 (DIN 1.4401) satin finish
- Blade wheel: AISI 316L (DIN 1.4404) mirror polished
- 6 blades to dispense a defined quantity of product
- Shafts without O-ring seals (0R)
- Materials:
- Stainless steel and silicone cuff
- GMP-compliant production
Product advantages:
- Small dimensions and low weight compared to conventional rotary valves
- Low friction due to minimal contact surface between rotor and seal
- Sterilizable in an autoclave
- Interchangeable
- No lubricant required
- Various sealing options (e.g. with FDA certificates)
- Easy to clean
The components of the SOLE VALVE®, TABLET VALVE® and ROTARY VALVE® are interchangeable without having to replace the entire unit. It is sufficient to replace the movable inner part and the outer body remains the same. This ensures maximum flexibility and low stock levels of spare parts.
Options:
- Double-acting stainless steel actuator,
- Electric and pneumatic drive,
- EX version,
- Further options on request
DOUBLE VALVE®
Especially for use in the food industry
The DOUBLE VALVE® flap valve serves as an interface to an automatically programmable weighing system.
The valve is fixed under the machine with a clamp and acts as an outlet opening. The valve controls the discharge of 95% of the weight by automatically opening the flap using a pneumatic drive.
It is operated by 2 double-acting drives made of anodized aluminium: 90° for the flap and 180° for the rotor.
Housing: AISI 316 L stainless steel
Seal: Silicone in accordance with FDA standard 177.260
The rotor for fine dosing can be customized with the number and volume of the piston pump according to customer requirements.
DOUBLE VALVE® is available in the following diameters:
- Flaps: 150, 200 or 250 mm
- Rotor: 80 or 100 mm
Transfer systems for the pharmaceutical industry
Transport / transfer systems for solids and liquids for use in the pharmaceutical industry. Particularly environmentally friendly, product-friendly and health and safety compliant.
BOLZ INTEC develops manually operated systems directly for operational practice in close cooperation with leading European pharmaceutical companies (R&D kilolab level). Each EPTS is custom-made and therefore always state-of-the-art.
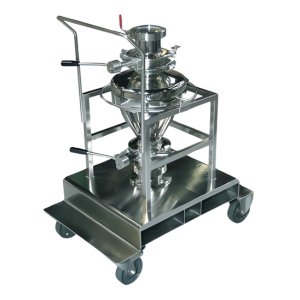
EPTS (Emission Free Powder Transport System)
for the closed transport of toxic media within a plant, e.g. from the weighing room to the reactor, with guaranteed emission-free product transport.
The system:
The EPTS consists of a container equipped with two flap valves attached to both openings. A funnel for filling and a CiP chamber for cleaning the entire system can be attached to the valve on the upper part of the container. The flap valve at the outlet of the transfer container is fitted with the respective connection of the reactor to be filled.
The active "clean-in-place system" ensures 100% emptying and enables the entire system to be cleaned without emissions. This ensures absolute employee and product protection.
The process flow:
Filling:
The filling funnel is flange-mounted on the upper part of the EPTS. The medium is then filled under a suction unit and weighed in. After filling, the flap valve is closed and the CiP chamber is refitted so that the EPTS can be moved to the reactor.
Problem-free filling:
When filled, the EPTS is docked onto the respective reactor, the powder is introduced into the subsequent process by opening the flap valve and applying a vacuum to the reactor. The "clean-in-place system" attached to the transfer system ensures that the entire system is subsequently cleaned without emissions. This ensures absolute employee and product protection.
As the EPTS and the reactor have the same specifications in terms of pressure and vacuum, necessary functions such as inertization and charging can be carried out under vacuum.
Technical features:
- Volume: 200 ml - 300 liters
- Pressure: Full vacuum / +1.5 bar
- Surface finish process side: RA'0.25μm Surface finish all others: RA ' 0.8 μm
both electropolished - Materials/process side: 1.4435 AISI 316L Hastelloy C 22 (optional)
- All others: 1.4301 AISI 304
- Seals: EPDM and/or PTFE (FDA-compliant)
Transfer system for lithium batteries
for the closed transport of carcinogenic media within a plant, e.g. from the weighing room to the reactor, with guaranteed emission-free product transport.
The system:The system consists of a container equipped with two flap valves attached to both openings. A funnel for filling and a CiP chamber for cleaning the entire system can be attached to the valve on the upper part of the container. The flap valve at the outlet of the transfer container is fitted with the respective connection of the reactor to be filled.
The active "clean-in-place system" ensures 100% emptying and enables the entire system to be cleaned without emissions. This ensures absolute employee and product protection.
The process flow:
Filling:
The filling funnel is flange-mounted on the upper part of the system. The medium is then filled under a suction unit and weighed in. After filling, the flap valve is closed and the CiP chamber is reassembled so that the system can be moved to the reactor.
Problem-free filling:
When filled, the system is docked onto the respective reactor, the powder is introduced into the subsequent process by opening the flap valve and applying a vacuum to the reactor. The "clean-in-place system" attached to the transfer system ensures that the entire system is subsequently cleaned without emissions. This ensures absolute employee and product protection.
As the system and the reactor have the same specifications in terms of pressure and vacuum, necessary functions such as inertization and charging can be carried out under vacuum.
Technical features:
- Volume: 200 ml - 300 liters
- Pressure: Full vacuum / +1.5 bar
- Surface finish process side: RA'0.25μm Surface finish all others: RA ' 0.8 μm
both electropolished - Materials/process side: 1.4435 AISI 316L Hastelloy C 22 (optional)
- All others: 1.4301 AISI 304
- Seals: EPDM and/or PTFE (FDA-compliant)
Containment up to OEB 4 in use:
- OEB = Occupational Exposure Band
- OEL = Occupational Exposure Limit
- AGW = occupational exposure limit value
- WG = active ingredient content
Laboratory cutlery made of low-ferrite stainless steel in accordance with GMP & FDA requirements
BOLZ INTEC manufactures laboratory cutlery for a wide variety of applications.
From spoons in various sizes to spatulas, double spoons and laboratory bowls, all models are made of high-quality stainless steel (1.4301 / 1.4401 / 1.4435 / 1.4571) or special materials such as Hastelloy.
Depending on requirements, the cutlery is available in different finishes, e.g. mill finish, brushed or electropolished. The marking, e.g. the batch or ID number, is applied in a place that is not in contact with the product.
The laboratory cutlery is resistant to acids, easy to clean and the electropolished finish creates a metallically clean surface, i.e. no risk of corrosion.
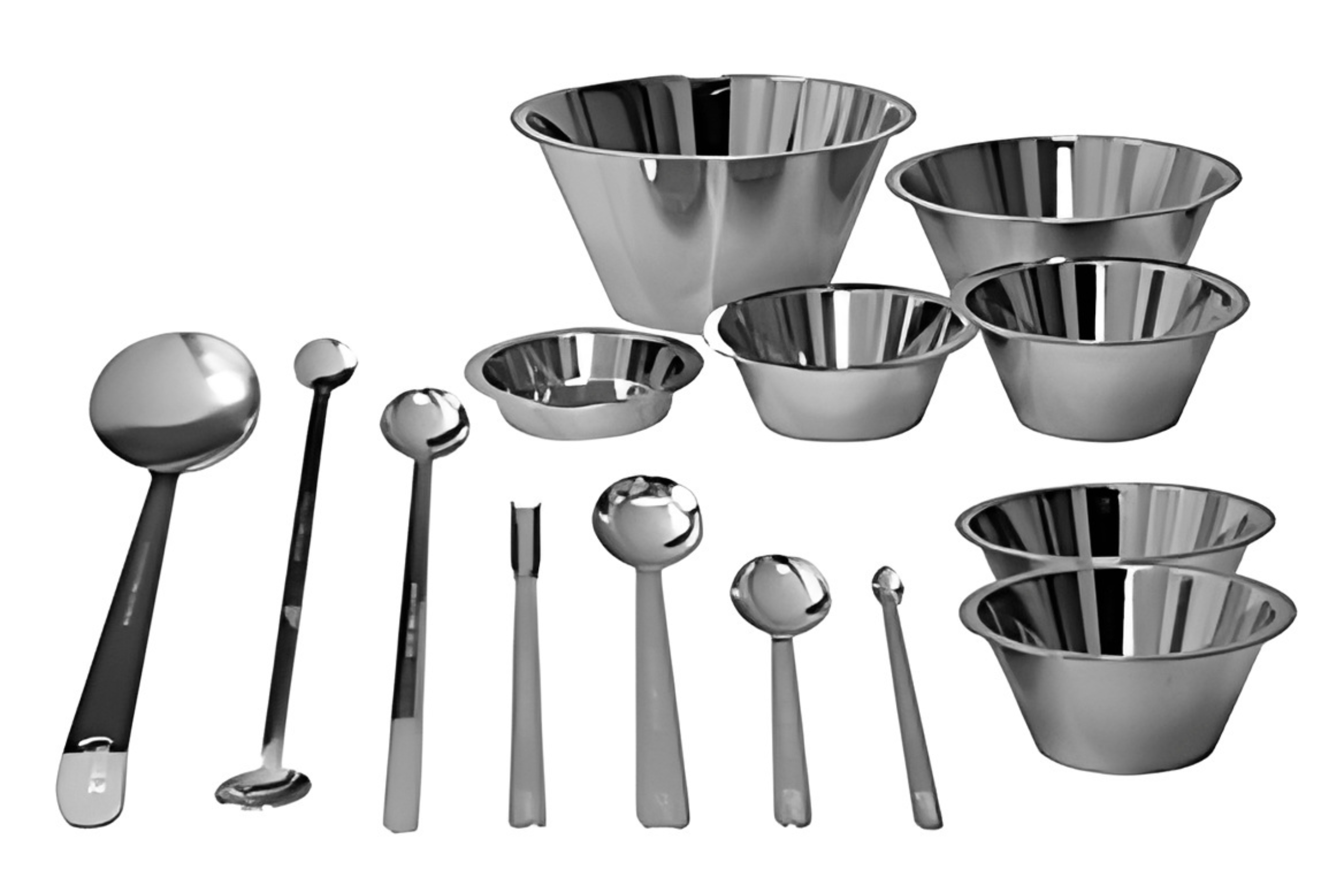
Spoon large
Spoon medium
Spoon small
Spoon small
spatula
Double spoon
U-filler 40/12/5
Spoon large
Spoon large
Diameter (d): 70 mm
Length (L): 285 mm
Material: freely selectable (1.4301/1.4401/1.4435/1.4571)
Electropolished
Marking handle top side
Article no.: 47001231
Spoon medium
Spoon medium
Diameter (d): 45 mm
Length (L): 180 mm
Material: freely selectable (1.4301/1.4401/1.4435/1.4571)
Electropolished
Marking handle top side
Article no.: 47001232
Spoon small
Spoon small
Diameter (d): 36 mm
Length (L): 135 mm or 250 mm
Material: freely selectable (1.4301/1.4401/1.4435/1.4571)
Electropolished
Marking on top of handle
Article no.: 47001233 or 47001234
spatula
Double spoon
U-filler 40/12/5
U-filler 40/12/5
Length (L): 175 mm
Material: freely selectable (1.4301/1.4401/1.4435/1.4571)
Electropolished
Marking on top of handle
Article no.: 47001237
Hand trowels
Bowls
Hand clamps made of low-ferrite stainless steel
The hand cones are available in a wide range of sizes. Ideal for use in laboratories in the pharmaceutical, chemical, cosmetics and food industries.
Technical data
Total length in mm 315
Diameter, handle in mm 18
Width of bucket in mm 100
Length of bucket in mm 160
Material: 1.4404/1.4435 - low ferrite, other materials on request.
The surface is finely ground and electrolytically polished, the Ra value is 0.6 μm. Laser marking is carried out according to the customer's individual specifications.
A factory acceptance certificate (WAZ 3.1.) can be supplied on request.
Conical bowls for the laboratory
These conical bowls with rim are available in a wide range of sizes and diameters. Ideal for use in laboratories in the pharmaceutical, chemical, cosmetics and food industries.
Technical data
Volume in liters 0.25 0.75 1.0 1.5 2.0 3.0 5.0
Diameter, top in mm 95 165 190 200 220 250 270
Diameter, bottom in mm 60 120 120 125 130 135 140
Height in mm 60 80 80 95 105 110 140
Material: 1.4404/1.4435 - low ferrite, other materials on request.
The surface is finely ground and electrolytically polished, the Ra value is 0.6 µm. Laser marking is carried out according to the customer's individual specifications.
On request, complete documentation in accordance with FDA and GMP regulations such as factory acceptance certificate (WAZ 3.1.), grinding, e-polishing and ferrite content report can be supplied.
All bowls can be stacked inside each other and therefore save space. They are very easy to clean.
Warum sich Kunden weltweit für unsere Sonderkonstruktionen aus Edelstahl entscheiden
Tradition & innovation since 1919
BOLZ INTEC specializes in the manufacture of stainless steel drums, pressure vessels, agitator vessels, transport containers and transfer systems for hygiene-sensitive industries.
High vertical integration
BOLZ INTEC has acquired outstanding expertise in the machining of stainless steels and special materials such as Hastelloy. Combined with the skills and abilities of our team, this enables us to achieve maximum vertical integration. All production steps are carried out in-house. BOLZ INTEC is therefore able to react extremely flexibly to customer delivery date requests and guarantee unique quality.
Customized solutions
Our design department designs, plans and develops practical products according to our customers' requirements. These include, for example, containers for pasty substances or liquids, transport containers for UN hazardous goods, cans for the storage and transfer of active ingredients, suction hoods for dust-free container loading and much more.
One-off production & small series
BOLZ INTEC also manufactures custom-made products and small series.
Machines for perfect surfaces
Nothing in the BOLZ INTEC machine park is off the shelf. From the deep-drawing press to the electropolishing system, we work with special machines that have been developed according to our own specifications in order to meet the highest standards of quality and precision.
Traceability & reproducibility
BOLZ INTEC's QM system and our intensive testing procedures ensure the consistent quality of the stainless steel surfaces manufactured by BOLZ INTEC. In this way, we make a decisive contribution to the traceability of products in critical industries.
Trust & security
Our striving for perfect quality, state-of-the-art production methods, but also craftsmanship and know-how are the basis for the superior BOLZ INTEC quality, which means safety and reliability for our customers. It is therefore not surprising that 80% of our customers have reordered every year for the last 10 years.
Comprehensive certification
We regularly have our quality certified externally: DIN 9001:2015, DIN EN ISO 3834-2:2006-03, DIN EN ISO 115085-2/CL1. We are a specialist company according to WHG §19/1 and carry out process tests according to DIN EN ISO 15614-1, operator tests according to DIN EN 1418. BOLZ INTEC fulfills the Pressure Equipment Directive-2014-68-EU/AD-2000 HPO and employs Intern. Welding engineers (DVS/IIW 1170).
High efficiency, low costs & great economy
Time savings in production
The use of stainless steel containers with optimized surfaces leads to significant time savings in the production process. By minimizing the build-up of materials, cleaning and maintenance times can be drastically reduced. This enables the containers to be reused more quickly and increases the overall efficiency of the production lines. In a production-intensive environment where time equals money, this time saving represents a significant economic advantage.
Reduced risk of production downtime
The reproducible quality of the stainless steel surfaces and the reduced number of defects minimize the risk of production downtime due to surface problems. This can lead to higher overall productivity and less downtime.
Reduction of production losses
Optimizing the container surfaces also minimizes the amount of product loss. Reduced adhesion means that more of the material produced is available for its intended use and does not end up as waste. This is a particularly important factor in industries where high-quality or very expensive materials are processed.
Improvement of product quality & product safety
Contamination-free production results in a higher quality end product. This is crucial in industries with strict quality and purity requirements, such as pharmaceuticals and food production, where purity and safety are top priorities. The use of optimized stainless steel containers can therefore also lead to improved brand image and customer satisfaction. We ensure the quality of our containers through our QM officer and stringent production processes. You will receive the corresponding documentation for each of our stainless steel drums.
Cost reduction through efficient cleaning & barrel maintenance
In addition to saving time, optimized surfaces also lead to a reduction in the costs of cleaning processes. Less build-up means less need for cleaning agents, water and energy. There is also less wear and tear on the containers themselves, which increases their service life and reduces the need for new purchases. In the long term, these savings in operating costs can make a significant difference to a company's profitability.
Longer container service life & positive eco-balance
The improved corrosion protection provided by the electropolishing process helps to extend the service life of stainless steel containers. Customers can thus reduce their costs for replacement investments and maintenance.
Customers from these industries increase their production efficiency with special stainless steel constructions from BOLZ INTEC
Reach your goal in just a few steps
Request
Send us an e-mail, give us a call or book an appointment via Calendly. In a phone call with one of our competent contacts, we will clarify a few questions in advance using checklists and send you a non-disclosure agreement (NDA).
Test phase
Based on your objectives and specifications, you will receive drums, containers, funnels and accessories from our test center - as required - to try out and test. You can use your test equipment to verify or adapt the specifications of your request.
Offer
During a visit to your premises, our competent contact partners will advise you on clarifying any final questions, finding solutions to identified problems and defining your exact requirements. We can then start production.
Our project team looks forward to your inquiry
Sie haben Fragen zu Sonderkonstruktionen, zu anderen Leistungen oder möchten von einem unserer kompetenten Mitarbeiter beraten werden?
Give us a call or send us an e-mail. We will make time for you and will be happy to call you back if you wish.
You ask, we answer
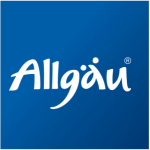
Sie haben Fragen zu Sonderkonstruktionen oder suchen Beratung?
Please do not hesitate to contact us by phone or e-mail.